In today's fast-paced work environments, ensuring safety is paramount. One of the critical components in maintaining a safe workplace is the use of equipment testers. These devices play a vital role in assessing the functionality and safety of various tools and machinery. But what exactly are equipment testers, and why are they so essential?
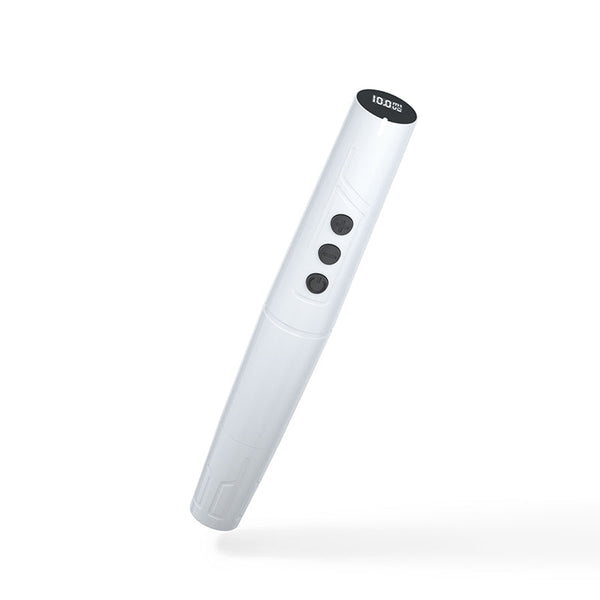
Understanding Equipment Testers
Equipment testers are specialized devices designed to evaluate the performance and safety of equipment used in various industries. They help identify potential hazards, ensuring that tools and machinery operate within safe parameters. This proactive approach not only protects employees but also minimizes the risk of costly accidents.
Types of Equipment Testers
There are several types of equipment testers available, each serving a specific purpose. Here are some common categories:
- Electrical Testers: These devices check the integrity of electrical systems, ensuring that they are safe to use.
- Pressure Testers: Used to assess the pressure levels in equipment, these testers help prevent leaks and failures.
- Calibration Tools: These ensure that measuring instruments provide accurate readings, which is crucial for compliance.
- Leak Detectors: Essential for identifying gas or fluid leaks, these testers are vital in maintaining safety standards.
The Role of Equipment Testers in Workplace Safety
Why are equipment testers so important in the workplace? The answer lies in their ability to enhance safety and compliance. Regular testing can:
- Identify potential hazards before they lead to accidents.
- Ensure compliance with industry regulations and standards.
- Extend the lifespan of equipment by identifying issues early.
- Promote a culture of safety among employees.
When equipment is regularly tested, employees can work with peace of mind, knowing that their tools are safe. Furthermore, companies that prioritize safety often see improved morale and productivity.
Best Practices for Using Equipment Testers
To maximize the benefits of equipment testers, consider the following best practices:
- Schedule regular testing intervals based on equipment usage.
- Train employees on how to use testers effectively.
- Document all testing results for future reference.
- Invest in high-quality testers to ensure accurate results.
For those in the tattoo industry, having reliable equipment is crucial. You can find essential that include various equipment testers to ensure safety and compliance.
Conclusion
In conclusion, the significance of equipment testers in ensuring workplace safety cannot be overstated. By regularly assessing the functionality and safety of tools and machinery, businesses can protect their employees and maintain compliance with industry standards. Investing in quality testing equipment and adhering to best practices will foster a safer work environment for everyone.