In the realm of modern manufacturing, selective laser sintering services have emerged as a pivotal technology for rapid prototyping. This innovative method utilizes a laser to fuse powdered materials, creating intricate and durable parts. But what makes this process so advantageous for businesses and designers alike?
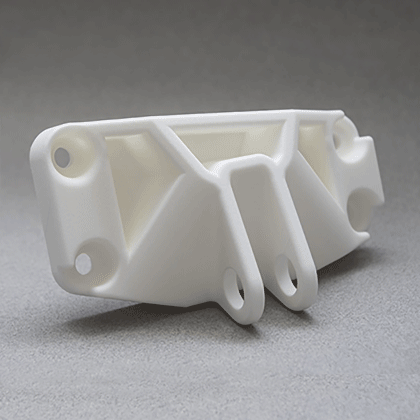
Understanding Selective Laser Sintering Services
Selective laser sintering (SLS) is a 3D printing technique that employs a high-powered laser to selectively fuse powdered materials, typically plastics or metals. The process begins with a thin layer of powder being spread across a build platform. The laser then scans the layer, fusing the particles together according to the 3D model's specifications. This layer-by-layer approach continues until the final part is completed. The result is a highly accurate and complex part that can be used for functional testing or as a final product.
Key Benefits of Selective Laser Sintering Services
- Design Freedom: One of the most significant advantages of SLS is its ability to create complex geometries that traditional manufacturing methods cannot achieve. This opens up new possibilities for innovative designs.
- Material Versatility: SLS can work with a variety of materials, including nylon, polyamide, and even metal powders. This versatility allows for the production of parts with different properties tailored to specific applications.
- Reduced Waste: Unlike subtractive manufacturing processes, SLS generates minimal waste. Unused powder can often be recycled and reused in future builds, making it an environmentally friendly option.
- Rapid Production: The speed at which SLS can produce parts is unparalleled. This rapid prototyping capability enables companies to accelerate their product development cycles significantly.
Applications of Selective Laser Sintering Services
So, where can selective laser sintering services be applied? The answer is vast. Industries such as aerospace, automotive, and healthcare have begun to leverage this technology for various applications:
- Functional Prototyping: Engineers can create prototypes that closely mimic the final product's performance, allowing for thorough testing and validation.
- End-Use Parts: In some cases, SLS parts are robust enough to be used directly in final products, particularly in low-volume production runs.
- Custom Tools and Fixtures: SLS allows for the rapid creation of custom tools, jigs, and fixtures tailored to specific manufacturing processes.
Conclusion
In conclusion, the benefits of selective laser sintering services for rapid prototyping are clear. From design freedom to material versatility, this technology is reshaping how industries approach product development. If you are interested in exploring more about 3D printing services, consider checking out for additional insights.