In the realm of modern manufacturing, fused deposition modeling services (FDM) have emerged as a pivotal technology. This innovative 3D printing technique allows for the creation of complex geometries and prototypes with remarkable precision. But what exactly is FDM, and how does it transform the prototyping and manufacturing landscape? Let’s delve deeper into this fascinating subject.
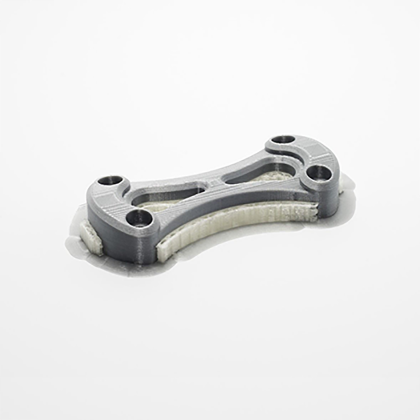
What is Fused Deposition Modeling?
Fused deposition modeling is a 3D printing process that involves the layer-by-layer deposition of thermoplastic materials. The process begins with a spool of filament, which is heated and extruded through a nozzle to create a three-dimensional object. This method is particularly popular due to its versatility and cost-effectiveness.
Key Benefits of Fused Deposition Modeling Services
- Cost-Effective: FDM is one of the most affordable 3D printing methods available, making it accessible for both small businesses and large enterprises.
- Material Variety: A wide range of thermoplastic materials can be used, including ABS, PLA, and PETG, allowing for flexibility in design and application.
- Rapid Prototyping: FDM enables quick turnaround times for prototypes, significantly reducing the time from concept to production.
- Complex Geometries: The ability to create intricate designs that would be challenging or impossible with traditional manufacturing methods is a significant advantage.
Applications of Fused Deposition Modeling Services
The applications of fused deposition modeling services are vast and varied. Industries such as automotive, aerospace, and healthcare have begun to embrace this technology for its numerous advantages. For instance, in the automotive sector, FDM is used to create functional prototypes and tooling, while in healthcare, it is utilized for custom medical devices and anatomical models.
How Fused Deposition Modeling Services Enhance Manufacturing
By integrating FDM into their workflows, manufacturers can achieve greater efficiency and innovation. The ability to quickly iterate designs allows for more experimentation and refinement, which can lead to superior products. Additionally, FDM can reduce material waste, as it only uses the necessary amount of filament for each print.
Choosing the Right Fused Deposition Modeling Service Provider
When selecting a provider for fused deposition modeling services, it is essential to consider several factors:
- Experience: Look for a company with a proven track record in FDM technology.
- Material Options: Ensure they offer a variety of materials suitable for your specific needs.
- Quality Assurance: Check if they have quality control measures in place to guarantee the integrity of the printed parts.
- Customer Support: A responsive support team can make a significant difference in your experience.
For those interested in exploring fused deposition modeling services, consider visiting for more information.
Conclusion
In conclusion, fused deposition modeling services are revolutionizing the way we approach prototyping and manufacturing. With its cost-effectiveness, material versatility, and ability to produce complex geometries, FDM is an invaluable tool for industries looking to innovate and streamline their processes. As technology continues to advance, the potential applications of FDM will only expand, making it an exciting area to watch.