Unlock the Secrets to Safer 3D Printing: Discover Game-Changing Solutions Today!
In recent years, 3D printing has revolutionized various industries by providing innovative solutions and unprecedented design freedom. However, as the technology becomes more accessible, the importance of safety in 3D printing safety environments cannot be overstated. With the rapid growth of this technology, users often overlook common risks and hazards associated with the process, which can lead to serious accidents or health issues. From toxic fumes emitted during the printing process to mechanical dangers posed by the equipment, understanding these risks is crucial. This article aims to highlight the significance of enhanced safety measures in 3D printing and to introduce you to products and services that can help create a safer working environment for all users.
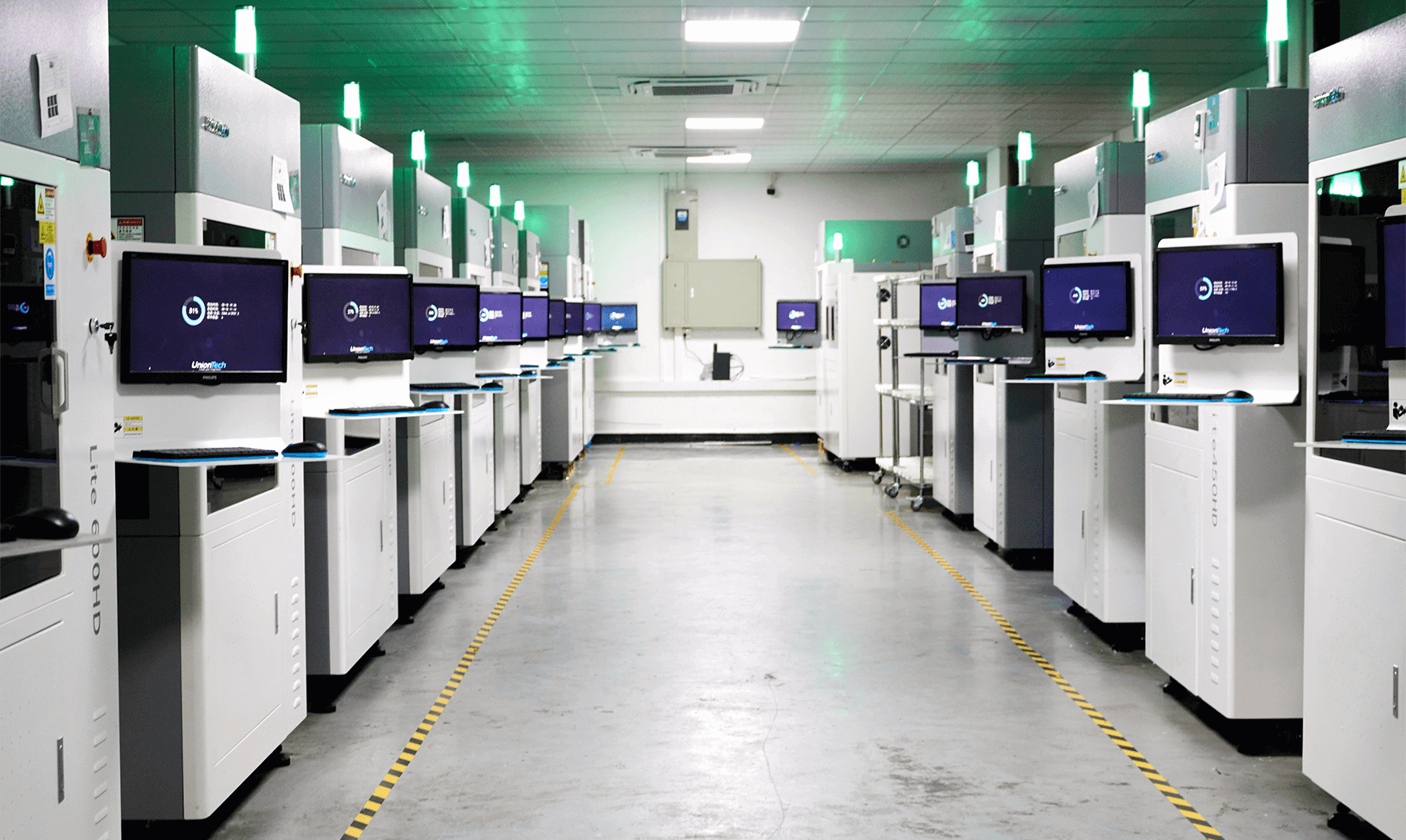
Understanding the Risks of 3D Printing
3D printing presents a unique set of risks that can impact both users and the surrounding environment. One of the most significant hazards arises from the materials used in the printing process. Many filaments, such as ABS and PLA, can release harmful fumes when heated, which can lead to respiratory issues if proper ventilation is not maintained. Additionally, the equipment itself poses physical risks. Users can suffer injuries from moving parts, sharp edges, or even burns from hot nozzles. A personal experience from a friend who works in a makerspace highlights this: during a busy session, a fellow user accidentally brushed against a hot nozzle, resulting in a painful burn and a reminder of the importance of awareness in such settings. Furthermore, environmental concerns, such as waste management and the disposal of toxic materials, must also be considered to ensure a safe and sustainable 3D printing practice.
Essential Safety Equipment for 3D Printing
To mitigate the risks associated with 3D printing, investing in essential safety equipment is vital. Personal protective equipment (PPE) is the first line of defense. Items such as safety goggles, gloves, and masks can protect users from harmful fumes and potential injuries. Ventilation systems, including fume extractors or air purifiers, play a crucial role in maintaining air quality by filtering out harmful particles and toxins. Moreover, fire suppression tools, like extinguishers specifically designed for flammable materials, should always be readily available in a 3D printing workspace. Each of these safety items not only protects the individual user but also contributes to a safer environment for everyone involved in the printing process. For instance, a colleague shared how installing an effective ventilation system in their workshop significantly reduced the number of headaches and respiratory irritations experienced by users.
Best Practices for Safe 3D Printing
Implementing best practices is essential for ensuring safety during 3D printing operations. Organizing the workspace can significantly enhance safety; ensuring that all tools and materials are neatly stored can prevent accidents and allow for quick access when needed. Proper machine handling is equally important—users should be trained to operate the equipment safely, including understanding emergency shut-off procedures. Regular maintenance of the printers is also critical; worn-out parts or malfunctioning equipment can lead to hazardous situations. Additionally, user training should encompass not only the operation of the machine but also the understanding of potential risks and the importance of using safety equipment. A friend of mine who runs a small 3D printing business emphasizes that regular training sessions have fostered a culture of safety and awareness among their team, resulting in fewer incidents and a more productive workspace.
Innovative Solutions for Enhanced Safety
As technology advances, innovative solutions continue to emerge, significantly improving safety in 3D printing. Automated monitoring systems can alert users to potential hazards, such as overheating or ventilation issues, allowing for prompt action to prevent accidents. Additionally, the development of advanced materials with lower toxicity profiles is paving the way for safer printing practices. These materials reduce the risk of harmful emissions without compromising print quality. Furthermore, safety-oriented design features, such as automatic shut-off mechanisms and enclosed printing areas, are becoming more common in new printer models, prioritizing user safety. The integration of these innovations can fundamentally change the landscape of 3D printing safety, creating a more secure and efficient working environment. A recent discussion with industry experts highlighted that incorporating these technologies not only enhances safety but also boosts confidence among users, encouraging more people to engage with 3D printing.
Summarizing the Importance of Safety in 3D Printing
In summary, prioritizing safety in 3D printing environments is crucial for protecting users and ensuring a sustainable practice. By understanding the risks associated with 3D printing, investing in essential safety equipment, implementing best practices, and embracing innovative solutions, users can create a safer workspace. As the technology continues to evolve, it is imperative that we remain vigilant and proactive about safety measures. By taking the necessary steps to enhance safety in 3D printing, we not only safeguard ourselves but also contribute to a culture of responsibility and awareness in the broader 3D printing community. Let us all commit to fostering a safer future in this exciting field.